Manufacturing is a never-ending cycle of production that needs to keep up with the increasing demands of an expanding market. It requires a workforce that never sleeps and supervisors that don’t sleep on the job of monitoring the time and attendance of employees.
Human resources have human frailties that can get them to the point of exhaustion. A better option is to automate time and attendance monitoring on shifting schedules especially for manufacturing companies that need to operate 24/7. As long as it is well-maintained and updated, an attendance software can help manufacturing companies in many ways, such as the following:
Facilitates efficient work scheduling
Ensuring that the right person is always at the right job at the right time is a challenge HR scheduling managers constantly face. Handling unscheduled absences and days off is distressing without a collaborative automated scheduling where both managers and employees coordinate and agree on availability.
Most automated attendance software allow managers to shift schedules or assign new employees using mobile devices such as Android tablets, iPads, iPhones, and smartphones. Scheduled changes are also available to employees anytime from anywhere.
Provides time management officers complete visibility over the shop floor
A time clock software eliminates the hassle of manually tracking employee attendance and monitoring activity in the shop floor from clock in to clock out. Managers can use GPS to verify employee location and make a run down if the right employee is doing the right task at the right time. Automating time and attendance monitoring also helps shop floor managers manage absences and tardiness to reduce the disruption of work shifts and save on labor costs.
Keeps employees engaged
An attendance software with an employee self-service feature allows employees to responsibly manage their availability for jobs assigned to them in coordination with their managers. Mobility is impacting the modern day workforce, including those in manufacturing, in ways that allow them to manage their time, attendance, work shifts, and vacation leaves without disrupting the flow of processes. They appreciate the ability to view their vacation and sick leave balance and request reasonable absences using their smartphones and other mobile devices. This leeway keeps them engaged and empowered, and serves as a motivation for improved efficiency and productivity.
Helps save on costs
Unauthorized overtimes, tardiness, prolonged coffee breaks, and other fraudulent time practices all contribute to unwanted labor costs. Shop floor managers are constantly looking for ways to maintain economic viability in an increasingly competitive manufacturing landscape. An automated attendance solution is a logical complement for better payroll management and helps eliminate costly time inaccuracies that undermine your company’s profitability.
Manual time and attendance management is an exhausting human resource task that can have a negative impact on overall efficiency and productivity. If you’re looking to improve the financial health of your manufacturing plant, an attendance software is the way to go.
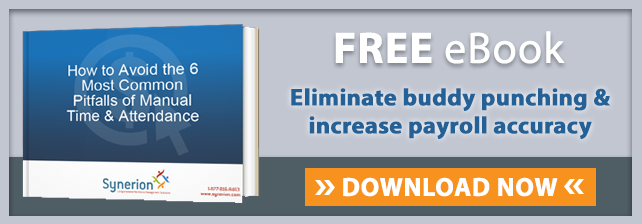