Labour costing makes up the bulk of company expenses yet too few businesses actually pay attention to those costs. Whether they think they have a system for detecting waste or they simply trust that their costs are in line with the competition, the result is the same: wasted time and wasted money.
Consider whether you're seeing these five signs of inadequate attention towards labour costing at your workplace.
You Don't Track Time Theft
If you think time theft isn't happening at your workplace, you're probably just not tracking it effectively. Time theft can cost employers over seven percent of payroll costs from things like buddy punching. Even honest employees can fall into the trap of clocking in a little earlier and clocking out when the time clock will round them up to the hour. A solution as simple as a timekeeping system can help reduce or even eliminate theft. Getting a handle on small transgressions can lead to big savings when it comes to labour costing by saving payroll dollars.
You Struggle to Attract New Employees
Finding reliable and skilled employees takes time and if your labour costing falls below industry average, it can be nearly impossible. A struggle to attract fresh talent isn't the result of a waning industry or a poor pool of talent. It often just boils down to your salaries and benefits being out of line with competitors. When businesses underpay their employees, they often have to hire more people to get the same job done effectively. A failure to attract prime candidates can be an early indicator that your labour costing isn't being appropriated correctly.
You Aren't Forecasting
The trick to managing labour costs isn't great guesswork: it's consistent forecasting. Carving out the time and using workforce management software can make forecasting pain-free but many companies don't set aside the time and suffer because of it. Determining months or even a year in advance how to staff your business can save money and eliminate labour waste. First understand the basics of forecasting, then use your workforce management software to determine your specific labour needs.
Your Managers' Schedules are a Mess
How concrete are your schedules? Many businesses use outdated forms of time keeping such as excel sheets or paper sheets to schedule employee shifts for the coming weeks or months. Unfortunately, with no paper trail or consolidated schedule, that schedule is often fluid resulting in managers forgetting to schedule requested time off. The end result is managers scrambling to find employees to cover and employees becoming frustrated with the lack of organization. Not only do companies pay for this disorganization in overtime but also in decreased employee morale. When schedules are sloppy, labour costing models are out of touch.
You Are Constantly Flexing or Short Staffed
Variations in workload isn't relegated to a single industry. Each industry struggles with consistency but smart companies can rise to that challenge. If you are consistently flexing employees or running short staffed, your labour costing model may be incorrect. By forecasting and delving into business data, even the most volatile companies can regulate their labour needs to reduce waste and ensure proper staffing at all times.
Labour costing isn't a one-time concern. To optimize workflow and reduce waste, companies need to constantly be assessing their labour costing model and refining it. If you're struggling with these five challenges, it's time to pay attention to your labour costing today.
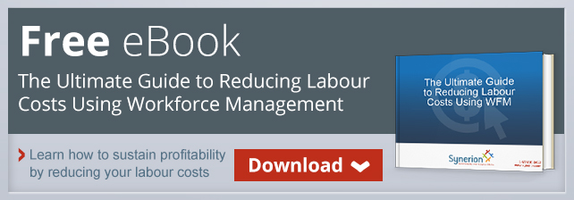