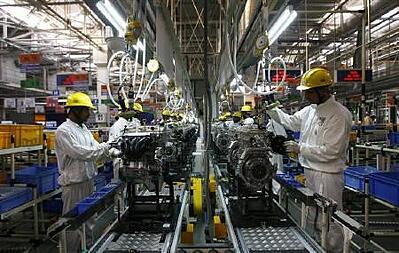
For those in the business of manufacturing, costs tend to run higher than in other industries due to its very nature. Material, equipment and labour costs are typically significant, and often these are the areas that have the greatest financial burden. However, there are ways to lower industrial costs that are sustainable and ultimately beneficial for the long-term health of the organization. Here are some of the most effective.
1. Go Lean
Though the concept of lean manufacturing has become somewhat of a buzzword, its impact on production costs is significant. Lean manufacturing is a term that describes the continual and relentless elimination of waste – and thus cost – from the entire production process. Under this definition, waste means anything or activity that does not add value. Typically, it aims to improve Overall Equipment Effectiveness and reduce the Six Big Losses: breakdowns, setup and adjustments, small stops, reduced speed, startup rejects, and production rejects (Source: Vorne).
Lean manufacturing can be implemented in a variety of ways, and most commonly involves a combination of process change, training, and data collection and analysis. More details on lean production implementation can be found in Reliable Plant’s 20 step road map.
2. Improve Labour Efficiencies
As mentioned above, labour costs can prove to be very high in the production industry. Too often, manufacturers looking to cut costs turn to layoffs or workforce downsizing, which is more of a short-term solution than a sustainable action. However, there are other ways to decrease labour costs and improve productivity that are more beneficial to businesses.
Better workforce management systems, for example, can serve to control labour and administrative expenses without the need for layoffs. In particular, they can help manage large amounts of employee time and attendance data, allowing organizations to:
- Automatically capture attendance/absence information
- Process data in line with labour laws and individual or collective agreements
- Prevent data entry and calculation errors via automation
- Transfer information to payroll and other necessary systems within the organization
Furthermore, because important information is centralized and many manual processes are automated, HR, operations and other managers are able to reduce daily administrative tasks and direct resources towards more role-critical work to help achieve business goals.
3. Invest in the Right Technology
In manufacturing, costs for equipment and technology tend to be very high, so investing in more may seem somewhat counterintuitive. However, making intelligent investments can save (and make) manufacturers a lot of money in the long-term. Depending on the nature of your organization, you can invest in anything from software to improve the design process, to automated inspection tools, to smart machines that support lean production.
Ultimately, reducing industrial costs comes down to the ability to identify issues that are costing money and/or reducing productivity, and working to correct them. The above tips are just a few ways manufacturers can begin this process in order to alleviate cost burdens affecting the health of their businesses.